Zero Liquid Discharge (ZLD) is no longer a futuristic goal—it’s an operational necessity for medium and large-scale industries navigating stringent environmental regulations and increasing water scarcity. ZLD is a wastewater treatment strategy aimed at eliminating any liquid waste leaving the plant, ensuring maximum water recovery and safe disposal of residual solids. While the concept is straightforward, successful implementation hinges on robust process design and the strategic selection of technologies tailored to the industry’s scale, effluent characteristics, and economic feasibility.
This blog explores the critical elements in designing ZLD systems and the technology options most suitable for medium and large-scale industries such as textiles, pharmaceuticals, chemicals, food & beverages, power, and petrochemicals.
Understanding the Need for ZLD
ZLD is a wastewater management approach that ensures no liquid waste is discharged into the environment. It involves the treatment and recovery of usable water from industrial effluents, while the remaining waste is converted into solid waste or reused in production cycles.
Industries generating high volumes of wastewater with toxic, saline, or heavy metal contamination are under increasing pressure to adopt ZLD systems due to:
- Regulatory compliance (CPCB, SPCBs, international norms)
- Corporate sustainability goals
- Water reuse demands
- Operational cost optimization over time
ZLD is particularly relevant for:
- Textile dyeing and finishing units
- Tannery and leather processing plants
- Power plants with high water withdrawal
- Chemical and petrochemical industries
- Pharmaceutical manufacturing units
Key Elements of ZLD Process Design
A well-engineered ZLD system comprises a series of stages, each customized for specific contaminant profiles and recovery goals. The process design includes:
A. Wastewater Characterization
Before any design begins, in-depth analysis of the wastewater is essential:
- TDS, COD, BOD, pH levels
- Presence of heavy metals, oils, and surfactants
- Flow variability over time
b. Segregation at Source
Different wastewater streams may need separate treatment. For instance, low TDS and high TDS streams should be handled differently to optimize cost and efficiency.
c. Primary & Secondary Treatment
These stages typically include:
- Screening, Equalization, Oil & Grease Removal
- Biological treatment (MBBR, SBR, ASP) for COD/BOD reduction
d. Tertiary Treatment
This involves polishing the effluent and reducing TDS through:
- Ultrafiltration (UF)
- Reverse Osmosis (RO) – single/multi-stage
e. Brine Management
Concentrated RO reject is handled using:
- Multiple Effect Evaporators (MEE)
- Mechanical Vapour Recompression (MVR)
- Agitated Thin Film Dryers (ATFD)
Technology Selection Criteria for ZLD
Choosing the right technology requires balancing technical, economic, and environmental factors:
i. Treatment Capacity
- Medium-scale plants (100–500 KLD): Modular RO systems, single-stage evaporators
- Large-scale plants (500 KLD–5 MLD+): Advanced MVR, multi-stage MEEs, centralized drying facilities
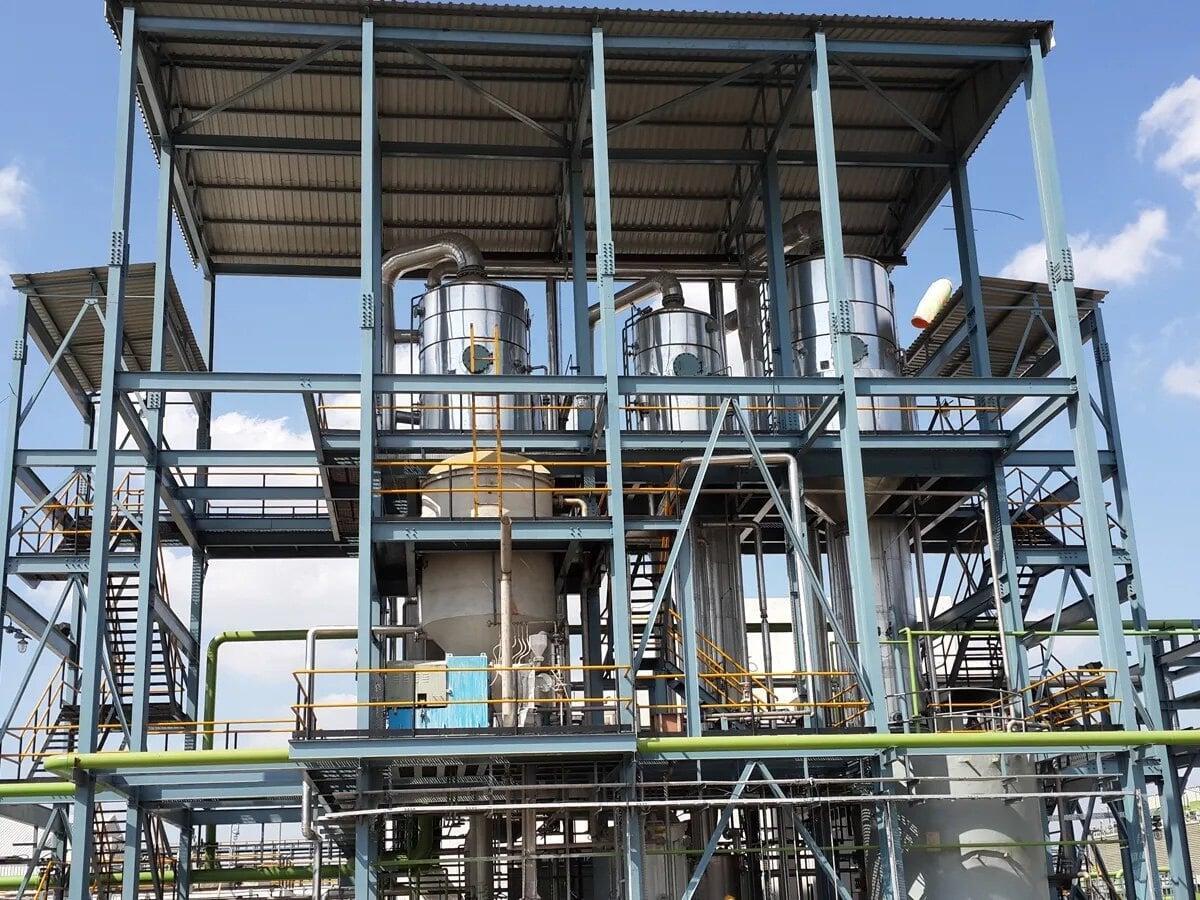
ii. Energy Efficiency
Energy consumption is highest in the evaporation phase. MVR is preferable for large-scale due to lower operational costs.
iii. Recovery Rates
RO systems can recover up to 80–85% of water. Combining multiple RO stages with softening and pre-treatment enhances efficiency.
iv. Salt Handling
Recovered salts can be recycled (in some industries) or need safe landfilling. Salt purity determines reusability.
v. Automation and Control
Smart PLC/SCADA systems ensure smooth operation and reduce manual dependency, especially in large-scale operations.
4. Industry-Specific Considerations
✅ Textile & Dyeing Units
High TDS and color removal is critical. Solutions include:
- Advanced oxidation processes (AOP)
- Nanofiltration + RO + MEE
✅ Pharmaceuticals
Complex organics and APIs require:
- Biological + chemical oxidation
- RO with high rejection membranes
- Incinerable solid residue handling
✅ Tanneries & Leather Units
High COD and chromium load:
- Chrome recovery units
- High-pressure RO and specialized chemical pretreatment
✅ Chemical & Petrochemical
Variability in load and toxicity:
- Continuous monitoring systems
- Custom resin-based polishing and robust evaporation technologies
5. Economic Feasibility and ROI
Initial ZLD system investment is high, but the long-term savings come from:
- Reduced freshwater dependency
- Reuse of recovered water
- Regulatory risk mitigation
- Energy and material recovery in large plants
For medium-scale plants, packaged ZLD systems with skid-mounted RO, small MEEs, and shared drying units can optimize CAPEX and OPEX.
Future Outlook
With increasing focus on sustainability, ZLD is being integrated with renewable energy solutions (like solar dryers) and AI-based control systems for predictive maintenance and energy optimization. Government incentives and ESG frameworks are likely to further drive ZLD adoption.
Innovations to Watch: ZLD at Delhi Water Expo 2025
The Delhi Water Expo 2025, organized by Water Today at ITPO, Pragati Maidan New Delhi from 21 -23 August 2025, is set to be a key platform for discovering cutting-edge ZLD technologies. Scheduled to bring together leading OEMs, system integrators, consultants, and end-users, the Expo will offer:
- Live demonstrations of modular ZLD units
- Presentations on reducing ZLD operating costs through energy-efficient evaporators
- Networking with technology providers offering custom ZLD packages for specific industrial applications
Whether you're planning a new ZLD plant or upgrading an existing one, the Delhi Water Expo is a must-attend event to evaluate solutions that match your industry’s size, needs, and sustainability goals.
Conclusion
Process design and technology selection are the backbone of any successful ZLD system. For medium and large-scale industries, the key lies in customization—there’s no one-size-fits-all solution. A holistic approach that considers wastewater characteristics, regulatory requirements, cost, and operational efficiency ensures sustainable and compliant operations. As industries embrace water stewardship, ZLD becomes a strategic enabler of both environmental responsibility and industrial resilience.